Steam Coil Air Preheaters Scaph Pdf
Posted By admin On 26.10.19Steam coil Air heaters’ (SCAPH) steam supply is kept isolated. From the air preheater as possible, to allow mixing of the flow to reduce temperature and 0. Mar 24, 2003 Steam Coil Air Heater (SCAH) Steam Coil Air Heater. The pressure test should be done as hydrotest with water in case of a steam coil.
Cold-end corrosion can occur on surfaces that are lower in temperature than the dew point of the flue gas to which they are exposed. Air heaters and economizers are particularly susceptible to corro sive attack. Other cold-end components, such as the induced draft fan, breeching, and stack, are less frequently problem areas. The accumulation of corrosion products often results in a loss of boiler efficiency and, occasionally, reduced capacity due to flow restriction caused by excessive deposits on heat transfer equipment. Acidic particle emission, commonly termed 'acid smut' or 'acid fallout,' is another cold-end problem.
It is caused by the production of large particulates (generally greater than 100 mesh) that issue from the stack and, due to their relatively large size, settle close to the stack. Usually, these particulates have a high concentration of condensed acid; therefore, they cause corrosion if they settle on metal surfaces. The most common cause of cold-end problems is the condensation of sulfuric acid. This chapter addresses problems incurred in the firing of sulfur-containing fuels. Sulfur in the fuel is oxidized to sulfur dioxide: S + O 2 = SO 2 sulfur oxygen sulfur dioxide A fraction of the sulfur dioxide, sometimes as high as 10%, is oxidized to sulfur trioxide. Sulfur trioxide combines with water to form sulfuric acid at temperatures at or below the dew point of the flue gas. In a boiler, most of the sulfur trioxide reaching the cold end is formed according to the following equation: SO 2 + 1/2 O 2 = SO 3 sulfur dioxide oxygen sulfur trioxide trioxide produced in any given situation is influenced by many variables, including excess air level, concentration of sulfur dioxide, temperature, gas residence time, and the presence of catalysts.
Vanadium pentoxide (V 2O 5) and ferric oxide (Fe 2O 3), which are commonly found on the surfaces of oil-fired boilers, are ef-fective catalysts for the heterogeneous oxidation of sulfur dioxide. Catalytic effects are influenced by the amount of surface area of catalyst exposed to the flue gas. Therefore, boiler cleanliness, a reflection of the amount of catalyst present, affects the amount of sulfur trioxide formed.
The quantity of sulfur trioxide in combustion gas can be determined fairly easily. The most commonly used measuring techniques involve either condensation of sulfur trioxide or adsorption in isopropyl alcohol. Higher flue gas moisture increases the dew point temperature for a given sulfur trioxide-sulfuric acid concentration. Cold-end metal temperatures and flue gas sulfur trioxide content can be used to predict the potential for corrosion problems. At the same sulfur content, gaseous fuels such as sour natural gas, sour refinery gas, and coke oven gas produce more severe problems than fuel oil. These gases contain more hydrogen than fuel oil, and their combustion results in higher flue gas moisture. Consequently, dew points are raised.
With any type of fuel, corrosion and fouling potentials rapidly increase below gas temperatures of 140 degrees F (60 degrees C), which is the typical water dew point for flue gases. Cold-end corrosion and deposition are usually much less severe in coal-fired boilers than in oil-fired units. Usually, coal ash is alkaline, so it increases the pH of the deposits formed in cold-end sections. Thus, the extent of the corrosive attack by sulfuric acid is diminished. Also, the high level of ash present when coal is fired results in a lower concentration of acid in the ash particle. At the same sulfur content, coal firing dew points are generally 20-40 degrees F lower than oil firing dew points.
The most common cause of deposition within air preheaters is the accumulation of corrosion products. Most air preheater deposits contain at least 60% iron sulfates formed by the corrosion of air heater tube metal. Therefore, a reduced corrosion rate frequently reduces the fouling of air preheaters. Air Preheaters A regenerative air preheater can reduce cold-end problems when installed instead of a recuperative air preheater on a new or existing boiler. In the regenerative air preheater design, heat transfer surfaces are below the acid dew point for much shorter periods of time.
Most modern regenerative air preheaters are equipped with steam or compressed air sootblowers and fixed or oscillating water washing nozzles. In boilers equipped with multiple units, individual air preheaters can be isolated and washed on-line. Suitable drain connections must be provided as well as a system for treating the wash water prior to disposal. Washing is generally continued until the pH of the wash water is above 4.5. The wash water effluent is a relatively low pH stream with a high soluble iron content. Most air preheaters are washed with untreated water. Some operators add caustic soda or soda ash to neutralize the deposits and lower the loss of air heater metal during washing.
The average cold-end temperature of an operating air preheater is the sum of combustion air inlet temperature and flue gas outlet temperature, divided by two. The average cold-end temperature is generally used in the assessment of potential problems and the selection of air preheater size and materials of construction. The average cold-end temperature of an operating air preheater must be maintained in accordance with the manufacturer's specifications. Corrosion-resistant materials are used in some regenerative air preheater cold sections to obtain the lowest possible stack gas temperature and consequently the highest boiler efficiency. Steam Coil Air Preheaters In some installations, heating coils are placed between the forced draft fan outlet and the air preheater inlet to accommodate seasonal fluctuations in incoming combustion air temperature. These heat exchangers are commonly termed 'steam coil air preheaters.' They maintain the average cold-end temperature of the air preheater above the acid dew point.
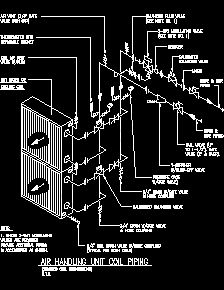
Where steam coils are used, the temperature of the combustion air entering the air heater is independent of the am-bient temperature. Preheaters are also installed when boilers are changed from coal or gas firing to oil firing.
Steam coils are installed because oil firing requires maintenance of an air preheater average cold-end temperature that is higher than that normally specified for the firing of natural gas or coal. The operation of steam coil air preheaters results in an increase in the heat rate of the steam plant. Combustion air bypasses around the air heater and hot air recirculation have also been used to control average cold-end temperatures. Both of these methods reduce boiler efficiency. Minimizing Air Infiltration. An experimentally determined relationship for one boiler is shown in Figure 22-2.
The infiltration of air into the flame zone or into an area where the catalytic oxidation of sulfur dioxide is occurring increases the potential for cold-end problems. Therefore, maintenance and inspection procedures should be directed toward minimizing air infiltration. Minimizing Flue Gas Moisture Content As previously stated, the dew point is not only affected by the partial pressure of sulfuric acid in the flue gas but also by the partial pressure of water in the flue gas. The minimum obtainable flue gas moisture content is determined by the moisture content of the fuel and combustion air and by the hydrogen content of the fuel. The moisture content of coal is somewhat controllable through proper handling and storage procedures.
Handling and storage specifications can be written limiting the moisture content of fuel oil. Factors that increase flue gas moisture content include: boiler tube leaks steam coil air preheater leaks excessive boiler or air heater soot blowing leaking water wash nozzles instrumentation leaks (such as coal and oil, oil and natural gas, or blast furnace gas and coke oven gas) must be fired simultaneously, certain ratios produce the highest dew points. The worst ratio on a Btu-fired basis is 1:1. When a fuel is fired that has a higher hydrogen content than the base fuel normally used, the flue gas produced has a higher moisture content, resulting in an increased dew point. When possible, fuels of different hydrogen content should be fired separately.
Many chemical solutions have been devised to control cold-end deposition and corrosion. These solutions can be divided into two broad classifications: fuel additives and cold-end additives. Fuel additives are compounds that are added directly to the fuel or combustion process. Cold-end additives are fed into the back of the boiler after steam-generating surfaces so that they spe-cifically treat only the lower-temperature areas. Fuel Additives Magnesium and magnesium/aluminum based fuel additives are used to reduce sulfur trioxide in the flue gas. These compounds function primarily by altering the effectiveness of the iron and vanadium catalysts.
They are fed to liquid fuels, most commonly residual fuel oil. Alkaline fuel oil additives, such as magnesium, also increase the pH of deposits formed on cold-end surfaces, thereby reducing corrosion. Cold-End Additives Cold-end corrosion and deposition can be controlled more economically and effectively through the use of cold-end additives.
Cold-end additives include sulfuric acid neutralizing agents and corrosion inhibitors. Magnesium Compounds. Alkaline magnesium compounds, such as magnesium oxide and magnesium carbonate, are fed to reduce the sulfur trioxide content of flue gases. These compounds are fed in high-temperature areas, such as primary superheater sections. The reaction product formed, magnesium sulfate, often increases deposition within air preheaters.
The main benefit of magnesium compound injection is a reduction in air preheater corrosion. Often, the level of fouling is not appreciably altered, because the corrosion product fouling is replaced by magnesium sulfate fouling. Therefore, where magnesium compounds are used, suitable water wash nozzles must be present to permit periodic removal of magnesium sulfate. Additives that remove sulfur trioxide from flue gas must be fed in stoichiometric quantities with respect to the amount of sulfur trioxide to be removed. Therefore, higher levels of sulfur in the fuel require higher feed rates for protection. Coal-fired boilers require less treatment than oil-fired boilers for a given sulfur level in the fuel.
Corrosion Inhibitors. Corrosion inhibitors can be added to the cold end of the boiler to alleviate problems associated with the condensation of sulfuric acid. These materials do not neutralize the sulfuric acid in the flue gas; they prevent surface corrosion where the sulfuric acid condenses. Fouling of the air preheater is reduced because the quantity of corrosion products is reduced.
Although the dosage of inhibitor required to achieve the desired effect increases with increasing acid content in the flue gas, the relationship is not linear. The compositions of inhibitor-type cold-end additives are usually proprietary. Products are available in powder and liquid form.
Liquid solutions are injected upstream of the problem area with atomizing spray nozzles. Justification for cold-end additives is generally based on the benefits obtained by higher unit heat rates and lower maintenance costs for the equipment in the cold-end section. The feed of cold-end additives enables the unit to operate with a lower rate of steam flow to the steam coil air preheaters, resulting in an increase in unit heat rate.
Steam Coil Air Preheaters
If average cold-end temperature is controlled with bypasses, the bypassed air flow can be reduced so that an improvement in boiler efficiency is obtained. A smaller improvement in heat rate is gained through reduction of fan horsepower, which reduces the average pressure drop across the air preheater. Acid Smut Control.
Cold-end additives can be used to reduce acid smut problems. In some in-stances, it is believed that smut is created when fly ash particles agglomerate to form larger particles.
These particles adsorb sulfuric acid mist and become highly acidic. Fly ash deposits often accumulate in low-temperature areas of breeching. During soot blowing or load changes, some of the deposited fly ash can be entrained in the flue gas stream and carried out the stack. The large particles then settle in the vicinity of the stack.
Magnesium-based fuel additives have been beneficial in reducing acid smut problems by increasing the pH of the deposits. Evaluation and Monitoring Techniques Corrosion Rate Measurement. Various devices are available to assess the impact of additive application on corrosion rates. Table 22-1 shows a selection of monitoring methods. In some cases, problems in the breeching, induced draft fans, and stack can be measured by corrosion coupons placed within the flue gas stream. For air heater corrosion and fouling problems, some provision must be made to maintain a corrosion specimen temperature that is within the ranges typically found in the operating air preheater. Corrosion probe methods (see Table 22-1) are used to simulate corrosion rates in an operating air preheater.
Schematic diagram of typical coal-fired power plant steam generator highlighting the air preheater (APH) location. An air preheater (APH) is any device designed to heat before another process (for example, in a ) with the primary objective of increasing the thermal efficiency of the process. They may be used alone or to replace a heat system or to replace a steam coil. In particular, this article describes the combustion air preheaters used in large found in producing from e.g.,.
The purpose of the air preheater is to recover the heat from the boiler which increases the thermal efficiency of the boiler by reducing the useful heat lost in the flue gas. As a consequence, the flue gases are also conveyed to the (or ) at a lower temperature, allowing simplified design of the conveyance system and the flue gas stack.
It also allows control over the temperature of gases leaving the stack (to meet emissions regulations, for example).It is installed between the economizer and chimney. Contents.
Types There are two types of air preheaters for use in steam generators in: One is a tubular type built into the boiler flue gas ducting, and the other is a air preheater. These may be arranged so the gas flows horizontally or vertically across the axis of rotation. Another type of air preheater is the regenerator used in iron or glass manufacture. Tubular type Construction features Tubular preheaters consist of straight bundles which pass through the outlet ducting of the boiler and open at each end outside of the ducting. Inside the ducting, the hot furnace gases pass around the preheater tubes, transferring heat from the exhaust gas to the air inside the preheater. Ambient air is forced by a fan through ducting at one end of the preheater tubes and at other end the heated air from inside of the tubes emerges into another set of ducting, which carries it to the boiler furnace for combustion.
Problems The tubular preheater ductings for cold and hot air require more space and structural supports than a rotating preheater design. Further, due to dust-laden abrasive flue gases, the tubes outside the ducting wear out faster on the side facing the gas current. Many advances have been made to eliminate this problem such as the use of ceramic and hardened steel. Many new (CFB) and (BFB) steam generators are currently incorporating tubular air heaters offering an advantage with regards to the moving parts of a rotary type. Dew point corrosion corrosion occurs for a variety of reasons.
The type of fuel used, its sulfur content and moisture content are contributing factors. However, by far the most significant cause of dew point corrosion is the metal temperature of the tubes. If the metal temperature within the tubes drops below the acid saturation temperature, usually at between 190 °F (88 °C)and 230 °F (110 °C), but sometimes at temperatures as high as 260 °F (127 °C), then the risk of dew point corrosion damage becomes considerable. Regenerative air preheaters There are two types of air preheaters: the rotating-plate regenerative air preheaters (RAPH) and the stationary-plate regenerative air preheaters (Rothemuhle). Rotating-plate regenerative air preheater. Principle function for the regenerative preheater. The rotating-plate design (RAPH) consists of a central rotating-plate element installed within a casing that is divided into two ( bi-sector type), three ( tri-sector type) or four ( quad-sector type) sectors containing seals around the element.
The seals allow the element to rotate through all the sectors, but keep gas leakage between sectors to a minimum while providing separate gas air and paths through each sector. Tri-sector types are the most common in modern power generation facilities. In the tri-sector design, the largest sector (usually spanning about half the cross-section of the casing) is connected to the boiler hot gas outlet. The hot exhaust gas flows over the central element, transferring some of its heat to the element, and is then ducted away for further treatment in and other equipment before being expelled from the. The second, smaller sector, is fed with ambient air by a, which passes over the heated element as it rotates into the sector, and is heated before being carried to the boiler furnace for combustion. The third sector is the smallest one and it heats air which is routed into the and used to carry the coal-air mixture to coal boiler burners.
Thus, the total air heated in the RAPH provides: heating air to remove the moisture from the pulverised coal dust, carrier air for transporting the pulverised coal to the boiler burners and the primary air for combustion. The itself is the medium of in this system, and is usually composed of some form of steel and/or structure. It rotates quite slowly (around 1-2 ) to allow optimum heat transfer first from the hot exhaust gases to the element, then as it rotates, from the element to the cooler air in the other sectors. Construction features In this design the whole air preheater casing is supported on the boiler supporting structure itself with necessary in the ducting.
The vertical rotor is supported on thrust bearings at the lower end and has an oil bath lubrication, cooled by water circulating in coils inside the oil bath. This arrangement is for cooling the lower end of the shaft, as this end of the vertical rotor is on the hot end of the ducting. The top end of the rotor has a simple roller bearing to hold the shaft in a vertical position.
The rotor is built up on the vertical shaft with radial supports and cages for holding the baskets in position. Radial and circumferential seal plates are also provided to avoid leakages of gases or air between the sectors or between the duct and the casing while in rotation. For on line cleaning of the deposits from the baskets steam jets are provided such that the blown out dust and ash are collected at the bottom ash hopper of the air preheater. This dust hopper is connected for emptying along with the main dust hoppers of the dust collectors.
The rotor is turned by an air driven motor and gearing, and is required to be started before starting the boiler and also to be kept in rotation for some time after the boiler is stopped, to avoid uneven expansion and contraction resulting in warping or cracking of the rotor. The station air is generally totally dry (dry air is required for the instrumentation), so the air used to drive the rotor is injected with oil to lubricate the air motor. Safety protected inspection windows are provided for viewing the preheater's internal operation under all operating conditions. The baskets are in the sector housings provided on the rotor and are renewable. The life of the baskets depend on the ash abrasiveness and corrosiveness of the boiler outlet gases. Problems The boiler flue gas contains many dust particles (due to high ash content) not contributing towards combustion, such as silica, which cause abrasive wear of the baskets, and may also contain corrosive gases depending on the composition of the fuel.
Steam Air Preheater
For example, coals generally result in high levels of and in the flue gas. The wear of the baskets therefore is generally more than other, cleaner-burning fuels. In this RAPH, the dust laden, corrosive boiler gases have to pass between the elements of air preheater baskets. The elements are made up of zig zag corrugated plates pressed into a steel basket giving sufficient annular space in between for the gas to pass through. These plates are corrugated to give more surface area for the heat to be absorbed and also to give it the rigidity for stacking them into the baskets.
Hence frequent replacements are called for and new baskets are always kept ready. In the early days, steel was being used for the elements. Today due to technological advance many manufacturers may use their own patents. Some manufacturers supply different materials for the use of the elements to lengthen the life of the baskets. In certain cases the unburnt deposits may occur on the air preheater elements causing it to catch fire during normal operations of the boiler, giving rise to explosions inside the air preheater.
Combustion Air Preheaters
Sometimes mild explosions may be detected in the by variations in the inlet and outlet temperatures of the combustion air. Main article: A consists of a brick checkerwork: bricks laid with spaces equivalent to a brick's width between them, so that air can flow relatively easily through the checkerwork.
The idea is that as hot exhaust gases flow through the checkerwork, they give up heat to the bricks. The airflow is then reversed, so that the hot bricks heat up the incoming combustion air and fuel. For a glass-melting furnace, a regenerator sits on either side of the furnace, often forming an integral whole. For a, the regenerators (commonly called Cowper stoves) sit separate to the furnace. A furnace needs no less than two stoves, but may have three. One of the stoves is 'on gas', receiving hot gases from the furnace top and heating the checkerwork inside, whilst the other is 'on blast', receiving cold air from the blowers, heating it and passing it to the blast furnace.
See also. External links. References.